Situation
Die Automobilbranche muss sich immer wieder strengeren Auflagen unterwerfen, was die Sicherheit und Qualitätskontrollen Ihrer Fahrzeuge betrifft. Dies hat zur Folge, dass eine verbesserte Qualität und Zuverlässigkeit der einzelnen Komponenten unabdingbar ist. Verstärkte Kontrollen und feinste Messtechnik werden dazu eingesetzt, um jedes einzelne Teil auf Herz und Nieren zu prüfen, bevor dieses für den Bau eines Fahrzeuges zugelassen wird.
Unser Kunde
MDS Maschinen- und Werkzeugbau GmbH & Co. KG ist seit über 50 Jahren Systemlieferant für automatisierte Verbindungstechnik. MDS bietet ganzheitliche Lösungen aus einer Hand und ist für die Herstellung von hochqualitativen Verbindungselementen bekannt.
Die verschiedenen Verbindungselemente wie beispielweise Einpress- oder Blindnietmuttern, Abstandshalter und verschiedene Bolzen werden einer rigorosen Qualitätsprüfung unterzogen. Alle Verbindungselemente werden, bevor sie an die jeweiligen Kunden gesendet werden, einer automatisierten 100% Prüfung bezüglich der optisch messbaren Maße unterzogen. Die Verbindungselemente werden von einem Kamerasystem bis in den 0,1 µm Bereich vermessen und automatisiert nach iO- und niO-Teilen sortiert.
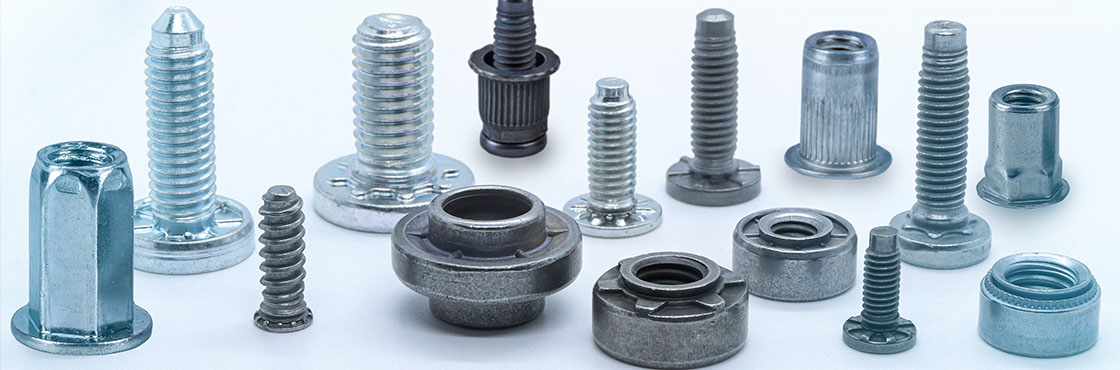
Herausforderung
Das momentane Messsystem konnte ein Verlaufen des Bandes nicht verhindern, wodurch es notwendig war, die Lage des Bandes permanent zu überwachen und regelmäßig manuell zu korrigieren. Darüber hinaus gab es durch das Verlaufen einen erhöhten Verschleiß der Bänder durch zusätzliche mechanische Belastungen an den Antriebsscheiben.
Die Herausforderung bestand darin, den Verschleiß der Bänder zu verringern und das Verlaufen der Bänder zu verhindern, um somit den Pseudo-Ausschussanteil der Messungen zu reduzieren. Da alle Pseudo-Ausschussteile wieder in das System eingespeist werden, um diese erneut zu vermessen, würde dies zum einen die Prozesszeiten verkürzen und zum anderen einen finanziellen Vorteil durch weniger Fehlteile bieten.
Lösung
In Zusammenarbeit mit MDS wurde die Prüfanlage auf Herz und Nieren untersucht. Hierbei stellte man fest, dass durch die vertikale Ausrichtung des Bandes und nicht ideale Rollenhalter, ein seitliches Verlaufen zum Einreißen des Lochmusters führte, da die Taktelemente auf die Lochkante trafen. Eine Taktung war jedoch gar nicht notwendig für die Messteile. Die Taktelemente wurden daher entfernt und ein blankes Band eingesetzt. Um den Bandlauf zu verbessern und das Band mittig zu führen, wurden nicht nur die Rollenhalter optimiert, um feinste Anpassungen des Winkels der Achse vornehmen zu können, sondern zusätzlich eine schmale Silikonbeschichtung mittig auf den Rollen angebracht. Diese zentriert das Stahlband und erhöht im Vergleich zu einer gekrönten Rolle dessen Biegebeanspruchung nicht weiter.
Zusätzlich bieten wir einen Laserzuschnitt des Bandes an, um die Toleranz der Kantengeradheit zu halbieren. Dies wird zusätzlich ein Anheben und Absenken der Muttern verhindern, welche hochpräzise auf der Bandkante durch die sensible Kameratechnik befördert werden.
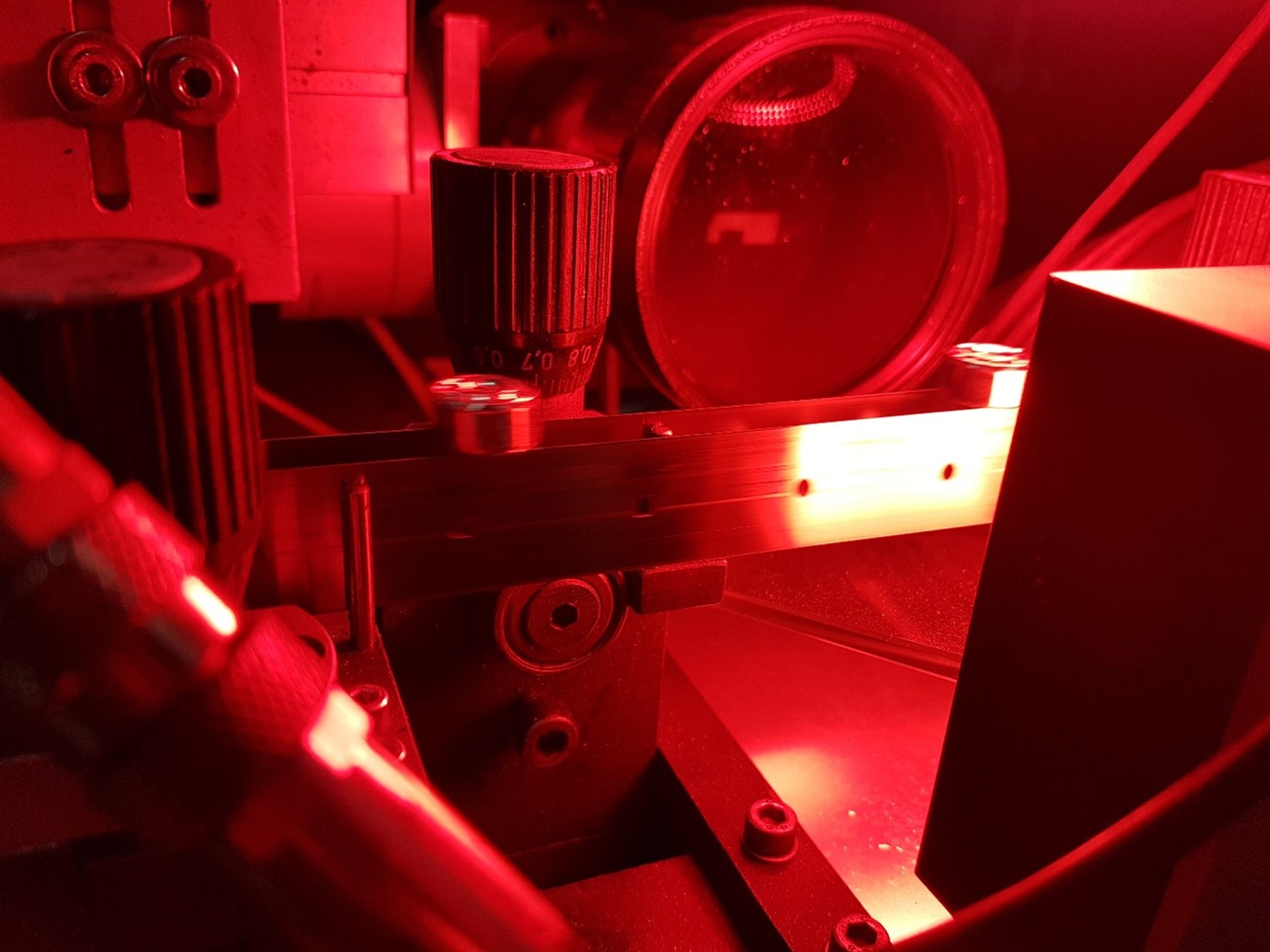
Resultate
Die Standzeit des Bandes wurde um ein vielfaches erhöht, während gleichzeitig die Prozesszeiten der Kameraprüfung der Verbindungselemente deutlich verkürzt wurden. Der Wartungsaufwand der Prüfanlage konnte durch die Optimierungen ebenfalls deutlich reduziert werden. Die Lieferung unserer Bänder mit präzisem Laserzuschnitt steht noch aus. Fest steht jedoch, dass in Zusammenarbeit mit uns deutliche Vorteile ermöglicht wurden und man an diesen Erfolg anknüpfen möchte.
Gerne dürfen Sie sich noch heute an einen unserer Vertriebsingenieure wenden, wenn wir Ihnen beim Einsatz eines Stahlbandes in Ihrer Anwendung behilflich sein können. Erfahren Sie mehr über unsere Stahlbandtechnologie auf belttechnologies.de.