Die ETH Zürich, eine der weltweit besten Universitäten im technisch-naturwissenschaftlichen Bereich und führende Universität in Kontinentaleuropa trat an uns für ein neues Forschungsprojekt in der Batterieproduktion heran. Herr Raphael Steffen vom Institut für Elektronik arbeitete eng mit seinen Kollegen zusammen, um eine schnellere und dadurch kosteneffizientere Methode zur Herstellung von Batterien zu finden. Aus den Fertigungsverfahren zur flüssigen Beschichtung von Oberflächen, hat die Vorhangbeschichtung das Potenzial, die Produktionsgeschwindigkeit der momentan verwendeten slot-die coating Methode (Schlitzdüsen-Beschichtung) in der Batterieproduktion zu überwinden.Source: https://www.sciencedirect.com/science/article/pii/S2589004221000237
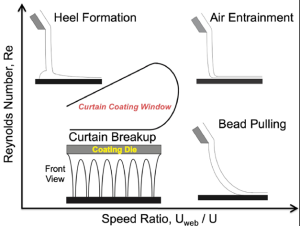
Vorhangbeschichtungsverfahren
Source: https://www.sciencedirect.com/science/article/pii/S0377025717305554
Die Vorhangbeschichtungsmethode erlaubt wie die Standardmethode, das Auftragen der aktiven Materialien, Anoden- und Kathodenmaterial, als Paste auf eine Aluminium- und Kupferfolie um daraus die Batterien zu fertigen.
Die Herausforderung bestand jedoch daraus, ein geeignetes Transportband zu finden, welches nicht nur hygienisch und leicht zu reinigen war, sondern auch aggressiven Chemikalien und hohen Temperaturen zur Trocknung standhalten konnte. Darüber hinaus ist ein schwingungsarmer Lauf von Vorteil, um die Batteriekomponenten sicher und genau zu transportieren und eine gleichmäßige Beschichtung auftragen zu können.
Herkömmliche Flachbandriemen kamen aufgrund Ihrer Zersetzbarkeit durch Chemikalien und Partikelgenerierung nicht in Frage. Nach langer Recherche fand Herr Steffen ein Bild eines Stahlbandes für die Schokoladenherstellung und machte sich auf die Suche nach uns.
Nach ausführlicher Betrachtung des Projektes, befanden wir ein Stahlband als optimale Transportlösung für die Vorhangbeschichtungsanlage.
Die gute Zusammenarbeit und stetige Kommunikation zwischen Belt Technologies und der ETH Zürich in diesem Entwicklungsprojekt führte zur Lieferung eines endlosverschweißten Edelstahlbandes und den dazugehörigen Antriebs- und Umlenkrollen aus Aluminium mit eloxierter Härtebeschichtung, welche in die von der ETH entworfene Transporteinheit verbaut wurden.
Die Qualität der Batterie ist dabei abhängig von einer präzisen und fehlerfreien Beschichtung. Dafür müssen die fluiddynamischen Eigenschaften der Paste entsprechend der neuen Methode angepasst werden. Die Aufgabe bestand nun darin eine CFD Simulation der Beschichtung durchzuführen, um damit das fluiddynamische Verhalten verschiedener Flüssigkeiten am Aufprallpunkt sowie eine laminare Verteilung über des Trägermaterials näher zu untersuchen. Experimentell wurden die Flüssigkeiten mittels Slot-Die Verfahren aufgetragen und verschiedene Beschichtungsstärken anhand der unterschiedlichen Geschwindigkeiten des Bandes bestimmt.
Die Ergebnisse der Untersuchung dienen als „proof of concept“ der Vorhangbeschichtungsmethode um verbesserten Taktzeiten zu ermöglichen.
Aufgrund der positiven Resultate lässt sich vermuten, dass Dank des flachen und robusten Stahlbandes, dünnere und weniger stabile Stromabnehmer (Folien) für die Beschichtung ausgewählt werden könnten. Dies würde erlauben „Dead weight“ in der Batterie zu reduzieren. (Source: https://www.sciencedirect.com/science/article/pii/S2542435121001501)
Zusammengefasst ist die Vorhangbeschichtungsmethode in Kombination mit dem Stahlband eine Möglichkeit um die chemische, thermische und mechanische Stabilität bei gleichzeitig erhöhter Produktionsgeschwindigkeit und somit bessere Kosteneffizienz für die Batterieproduktion zu ermöglichen.
Typischer Aufbau einer Batterie (Source: https://www.nature.com/articles/s41467-019-09933-0)
Könnte das Stahlband die Zukunft der fortschrittlichen Batterieproduktion sein?
Entscheiden Sie selbst und wenden Sie sich noch heute an unsere Vertriebsingenieure.